
BW Ultra
A reliable multi-gas monitor for confined spaces.

BW Ultra
BW Ultra is a reliable and user-friendly way for oil & gas workers to sample and monitor confined spaces and prevent safety incidents.
Scope
User testing
Concept Development
Dev handoff
Documentation
My role
UX Design
UI Design
UX Research
UX Copy
Interaction design
Information Architecture
Translations
Duration
Dec 2015 - Aug 2016
Stack
Axure
Ilustrator
Jira
Visio
Easy-GUI
WHAT I WAS ASKED TO DO
-
Design and define UI patterns for a GUI meant to be rendered in 7 languages
-
Update and expand an icon set
-
Generate UI flows and GUI guides for firmware developers located both in Canada and India.
THE RESULTS
-
GUI got awarded 2 US patents
- Usability tests at the Wichita State University showed an improved reaction time to a potential gas event by 60%.
- UI patterns are part of the visual design language for other multigas monitors, like Honeywell RigRat.
- The customer journey map and experience map are now used as a baseline for future projects within the gas detection portfolio.
The approach
Getting insights to better understand the problem
Discover | Define | Ideate | Prototype | Evaluate | Deliver
Stakeholder evaluation: What do we want to do? Why? Who are our competitors? What are the technical limitations? Metrics.
Method: Stakeholder interviews, evaluation of the statement of requirements, competitive analysis, heuristic evaluations.
User research: Who uses a multigas monitor? Where and how do they use these monitors? What are they currently using and why? What are their goals, needs and current frustrations?
Methods: Contextual inquiry, Field studies, Diary studies.
Alliance with the Product Marketing Manager was crucial to getting in touch with the right users. I also created templates for interviewing stakeholders, documenting competitive analysis and heuristics evaluations.
status quo
The competition


Our user base environment



Discover | Define | Ideate | Prototype | Evaluate | Deliver
Clear understanding of the problem, the goal and the users.
Understanding the problem: Our current offering was over a decade old, parts were becoming obsolete, users preferred competitors because they were perceived as easier to use and service.
Methods: Insight prioritization, Affinity maps, "how may we" questions
Understanding the user: From novice to experts, from highly skilled individuals that care about their team safety to amateurs attracted by a beefy paycheque without explicit experience. Portable gas monitors are just another piece of equipment to wear to be able to do the job, as long as users don't get an alarm they can keep doing their job, other feedback is largely ignored. Downtime at gas plants means loss of productivity and profits as well as time away from family.
Methods: Personas, Experience map, User journey map, User stories
Hypothesis: Companies are loose millions on revenue every time there's a false alarm (cause workers have to stop and evacuate). What If users don't have to stop working for long periods or at all?
Building relationships with product testers, QA leads, service staff, procurement staff and regulatory bodies was paramount to understand hardware limitations as well as identifying gaps for technology research needed to be done. I created a set of personas as well as a journey map and experience map.
Personas
As part of my user research I joined a confined space training. It is an in-class 8-hr training with no pre-requisites, but it is a mandatory training for confine space entry and hole watch operations.
I've never worked in an oil field. The guy to my right just got the job and was leaving the next morning to an oil field up north, he had no idea of at what levels of O2 his gas monitor will go into an alarm. The guy to my left had been in oil rigs most of his life, he's a pro and knows that alarm levels are set differently depending on the company and on the specific sites he works at. The three of us got a certificate after the training.
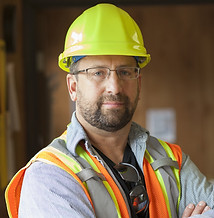
Peter, 45
Seasoned oil and gas worker, has done it all from sour gas plants to confined spaces. He takes this training as a refreshment for his own safety, he tries to keep up with new gas monitoring technologies and regulations.

Alejandra, 32
UX designer in the search of better understanding of why, who and how a gas monitor is used in confined spaces and hole watch operations.

James, 22
Previously a line cook, heard pay is great up north. Has no experience with gas detection and he needs to pass this training to be able to start his hole watch duties immediately.

-
He's currently working in confined spaces and even if he doesn't need to update his training, he likes to stay up to date with the latest technologies and regulations.
-
He works solo and on a team depending on the job and the site.
-
Sometimes he has to work with people that had never been to an oil rig.
-
Often times he has to stay on-site to finish a job that got interrupted because of a false alarm or a true evacuation situation.
-
Most of his daily shifts are16hrs, even if nothing goes wrong.
Tasks
Steve, 52
Steve is a Safety lead, started his career at 20, when he moved from Northern Ontario to Calgary knowing he could make enough to pay for his student loan. He's got 3 children and a wife that he sees every two weeks if everything is well at his plant.
-
Monitor confined spaces so other teams can do their jobs
-
Hole watch
-
Mentor junior workers
Goals
-
Keep himself and his crew safe
-
His crew knows what to do when their monitors go in alarm
-
Finish the job. Be home every 2 weeks as expected
Needs
-
Monitors to be readily available and in good working state at all times.
-
His crew to be properly trained in the equipment itself and the site's own specifications and evacuation protocols
Frustrations
-
Amateur coworkers don't know industry standards, nor the number that would set their monitors in alarm.
-
Broken monitors take too long to get back into the field.

Journey map
I took a holistic approach, starting with the end user's motivation. Traversing from the point of engagement to upsell, mapping out the key activities.
Identifying and involving each of the stakeholders that had and active touch-point in the journey.
Layering with a 5 start experience evaluation, pointing out critical factors leading to both a positive and a negative end-to-end user experience.
It was a full team effort to pull this off, literally everyone from the receptionist to training staff to oil rig worker and office staff contributed to this by participating in interviews and workshops.
Discover | Define | Ideate | Prototype | Evaluate | Deliver
Find solutions to the problem with the insights.
Brainstorming workshops: Round robin, Affinity diagrams, "How may we", Rose/thorn/bud
Artifacts: Storyboards, UI flows, Mind maps


Discover | Define | Ideate | Prototype | Evaluate | Deliver
Build and test ideas. Fail to succeed!
Paper prototype: Quick & dirty, interaction simulation, identification of main GUI elements, test. Repeat.
Wireframes: B&W skeletons, detailed user flows and interactions, test. Repeat.
Hi-Fidelity prototypes: Mockups, interactive prototypes, micro-interactions. Repeat.
Partnering with WSU to outsource usability testing was key to gaining by in and getting the LCD that would work best for the project vision. I created the outline for the test script, as well as the graphical assets to be evaluated.
BREAKING PARADIGMS
How to design an intuitive GUI that serves a user base that is so diverse? From novice to experts, from workers that care about their safety and others to others that seem to only care about the money.
Breaking the paradigms of our existing UX patterns and asset libraries was a challenge when the devices in question have to undergo heavy regulatory tests. Regardless of what the user research shows, if the equipment I recommend does not pass the regulatory test, there's no way it will even be considered. Since the LCD unit was the bulk of the cost to produce a gas monitor, there had to be a strong business case to use anything beyond the status quo. I had to support every decision I made with data throughout the process.

[UX] - How about a full colour dot matrix display?
[Marketing/Engineering] - Not good enough under extreme weather

[UX] - How about a full dot matrix display?
[Marketing/Sourcing/Engineering] - Yes, great idea!
[UX] - Here is one that costs twice as much!
[Marketing] - Show me the value.
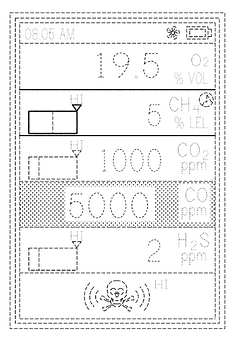
[UX] Let's add a hole watch mode to increase chances of users noticing gas rising/dropping at a glance.
[Marketing] - Yes, it could be a premium feature.

[UX] Let's visualize and test different options for that Hole Watch mode

[UX] - How about offering both dark and light themes? Most users identify with the gadgets they commonly use, like their mobile phones.
[Marketing] - Yes, it could be a premium feature.
Create documentation and work with Devs to implement keeping design intent
Discover | Define | Ideate | Prototype | Evaluate | Deliver
Artifacts: Detailed UI flows, IA tables, String & translation tables, Graphic assets, Red line mockups, Style kits, Help documentation, Technical writing.
As part support implementation, I conducted a workshop to explore easyGUI and make the handoff to firmware engineers easier. I also create the assets to be used in help documentation and put together the regulatory sticker while we were on the process of hiring a new tech writer.

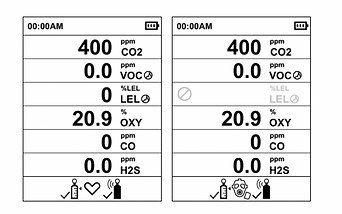

THe results
BW Ultra was awarded with 2 US patents for the GUI I designed. Usability tests showed an improved reaction time to a potential gas event by 60%. The GUI allows users to activate a hole watch mode that gives gas readings at a glance without having to know what the reading itself is. Our users can now plan ahead instead of simply react when an alarm goes off.
BW Ultra GUI is the base for other gas monitors like Honeywell BW RigRagt
D800760 S1
WO/2017/147360

